ACCELA COTA PRO
Doubling Your Tablet Coating Productivity
Thomas Processing built the foundation for the ACCELA COTA PRO with the introduction of the original Accela-Cota system in 1968. Today, Thomas’s ACCELA COTA PRO is evidence of our passion for building on the tradition of innovation.
One of ACCELA COTA PRO’s game-changing differentiators is its cylindrical (C) drum. Traditional coaters rely on a biconical (B) drum designs. When you compare it with the ACCELA COTA PRO B drum, the C drum design matches the same 60-inch diameter but provides a 35% higher capacity with a 700-liter capacity drum.
- Flush-mounted solution-delivery components for unparalleled access and cleanability
- Reduced installation space
- Highly accurate flowmeter for solution flow control
- Sanitary peristaltic pump
- Right-hand or left-hand mounting configuration
- Streamlined sanitary design
- Eliminates air and solution lines over spray zone
- Patented Thomas Spray Bar with anti-bearding nozzles
- Independent control of pattern and atomizing air
- Tool-less maintenance
- Modular ergonomic design
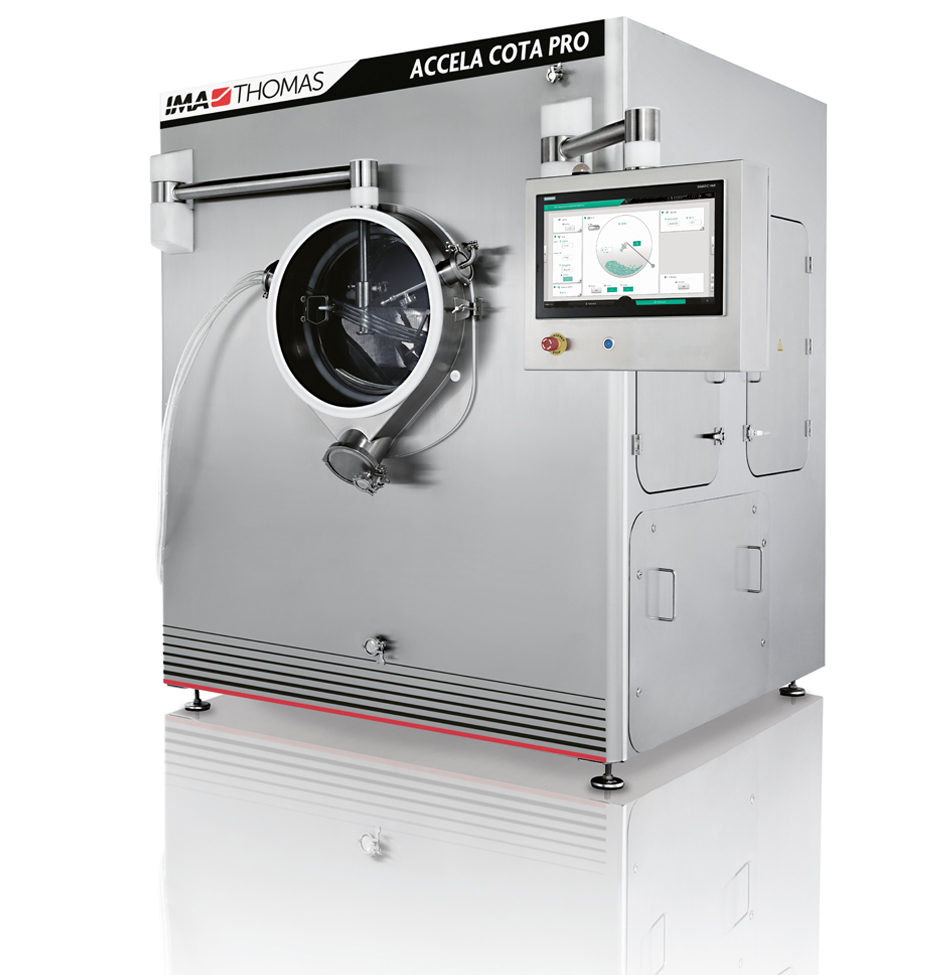
ACCELA COTA PRO Drums
- 48B Biconical Drum [40-190L]
- 48C Cylindrical Drum [50-250L]
- 48XC Cylindrical Drum [80-325L]
- 60B Biconical Drum [115-460L]
- 60C Cylindrical Drum [100-500L]
- 60XB Biconical Drum [130-530L]
- 60XC Cylindrical Drum [180-700L]
Double Your Coating Room Productivity With the ACCELA COTA PRO
Thomas’s ACCELA COTA PRO process improvements boost the performance of every batch you coat, every day.
Comparing the Performance of the Typical Batch Coater
We looked at the original ACCELA COTA system and our FLEX line of coaters and put their best features into the ACCELA COTA PRO, finding innovative ways to make the most of the interior space to increase productivity.
The cylindrical drum provides a much larger perforated area, which means more airflow across the tablets. Traditional systems are often designed with a 4,000-cfm air handling system, but our ACCELA COTA PRO with the cylindrical drum is equipped with a 7,000-cfm air handling system.
The increased perforated area allows us to increase the typical number of spray guns with the Thomas Spray Bar. The drum design also incorporates our Helical Baffles, which provide optimized mixing. With all these design features, we can achieve a higher spray rate, which equals shorter batch times across the board.
Faster Coating, Shorter Batch Time
Based on real-world batch data and our Thermodynamic Analysis of Aqueous Coating (TAAC) model, we predicted the average batch times for a traditional batch coater and compared it to standard coating machines, giving you accurate, time-saving results.
With the following calculations,
- 0.75 kg/liter bulk density
- 65 Celsius inlet temperature
- 10 Celsius dew point
- 3% weight gain
- Aqueous coating solution
- 20% solids
- EEF 3.25
We predict the following results that add up to a 75% increase in productivity:
Traditional Batch Coater Times
Batch Size | Load | Spray | Unload |
---|---|---|---|
375 kg | 20 min | 72 min | 25 min |
Productivity | Warm Up | Cool Down | Total Batch Time |
180 kg/hr | 5 min | 5 min | 127 min |
ACCELA COTA PRO Coater Times
Batch Size | Load | Spray | Unload |
---|---|---|---|
500 kg | 15 min | 55 min | 15 min |
Productivity | Warm Up | Cool Down | Total Batch Time |
318 kg/hr | 5 min | 5 min | 95 min |
Start Your Partnership Today
We have a tradition of building innovative machines that lead to long-standing customer partnerships. Contact us today to start your tablet coating journey with us.
About Us
Thomas Processing, formerly known as Thomas Engineering, provides high-quality tablet coating systems and expert solutions to manufacturers across the globe. With more than 60 years of experience, we design our machines based on what works best with modern coating advancements.